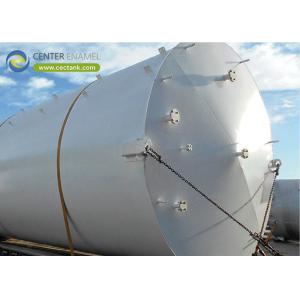
Add to Cart
Center Enamel: Optimizing Catalytic and Reaction Processes with Fluidization as a Leading China Fluidized Bed Reactor Manufacturer
In the dynamic landscape of chemical, petrochemical, energy, and environmental processing, fluidized bed reactors stand as a powerful and versatile technology. Their unique ability to suspend solid particles in a gas or liquid stream creates exceptional mixing, heat and mass transfer characteristics, and precise temperature control, making them ideal for a wide range of catalytic and non-catalytic reactions. From catalytic cracking in refineries and combustion of solid fuels to polymerization and drying of particulate materials, fluidized bed reactors play a crucial role in enhancing efficiency, selectivity, and throughput. At the forefront of China's fluidized bed reactor manufacturing industry stands Shijiazhuang Zhengzhong Technology Co., Ltd (Center Enamel), a national "little giant" enterprise recognized for its specialization, innovation, and unwavering commitment to quality. Integrating in-house R&D, meticulous design, advanced manufacturing, and comprehensive sales, Center Enamel has firmly established itself as a leading China fluidized bed reactor manufacturer, providing a comprehensive portfolio of robust and high-performance reactors and unparalleled technical expertise to a diverse range of industries.
For decades, Center Enamel has been dedicated to the independent design, production, and manufacturing of a diverse range of process equipment. Recognizing the significant advantages of fluidization technology for various industrial processes, we have cultivated deep expertise in the design and fabrication of high-performance fluidized bed reactors. Our focus extends across industries including petrochemicals (catalytic cracking, reforming), energy (coal combustion, gasification), chemicals (polymerization, calcination), environmental (wastewater treatment, catalytic oxidation of pollutants), and more, enabling us to engineer bespoke fluidized bed reactor solutions that precisely address the unique and often demanding requirements of these complex processes. Guided by our core values of "quality, sincerity, friendship, progress and innovation," we actively champion development and innovation, consistently prioritizing customer needs in every facet of our operations. Our relentless pursuit of product excellence and technological advancement ensures that we continuously enhance our capabilities, empowering us to wholeheartedly deliver superior fluidized bed reactor solutions and comprehensive support to our esteemed clientele.
Engineered for Optimal Solid-Fluid Interaction: Tailored Fluidized Bed Reactor Solutions Through Innovative Design
At Center Enamel, we recognize that effective fluidized bed reactor design demands a comprehensive understanding of fluid mechanics (gas or liquid flow through particle beds), particle dynamics, heat and mass transfer in fluidized systems, chemical reaction engineering (catalysis, combustion), material science (erosion resistance), and safety considerations for handling particulate solids and reacting fluids. The diverse nature of fluidized bed applications, varying particle sizes and properties, and the characteristics of the fluidizing medium and reaction chemistry necessitate tailored solutions. In response to these varied and often demanding requirements, our design philosophy is anchored in high-standard engineering, driven by a commitment to crafting exclusive fluidized bed reactors meticulously adapted to each customer's unique application and operating conditions. Our engineering approach meticulously considers the critical factors that govern stable and uniform fluidization, efficient contact between solids and fluids, effective heat transfer to and from the fluidized bed, controlled residence time of solids and gases, prevention of particle attrition and elutriation, robust containment under operating pressure and temperature, material compatibility with the process chemistry and abrasive solids, and efficient solids handling systems (feeding and withdrawal).
During the design phase, we conduct a thorough analysis of the process requirements, meticulously evaluating the reaction kinetics, catalyst or solid particle properties (size distribution, density, shape, attrition resistance), fluidizing medium properties (viscosity, density), flow rates, operating temperature and pressure, heat transfer requirements, and any specific needs for staged fluidization or internal structures. Our design process involves selecting the appropriate reactor geometry (vertical cylindrical, conical), distributor plate design (to ensure uniform gas or liquid distribution), reactor diameter and height (optimized for residence time and fluidization regime), internal structures (e.g., baffles, cyclones for particle separation, heat transfer surfaces), and solids handling systems (feeders, discharge valves). We carefully consider the fluidization regime (bubbling, turbulent, fast fluidization) based on the application and particle characteristics. For catalytic reactors, we optimize catalyst distribution and minimize deactivation. For combustion applications, we ensure efficient mixing and complete combustion. Furthermore, safety considerations related to handling potentially flammable or hazardous materials are paramount in our design. The ease of maintenance and accessibility for inspection and repair are also integral to our design. This holistic design methodology guarantees that every fluidized bed reactor leaving our facilities is engineered to deliver exceptional process performance, efficiency, and reliability for its intended application.
Precision in Production: Crafting Excellence in Every Fluidized Bed Reactor
The efficient and safe operation of a fluidized bed reactor, often involving high temperatures, pressures, and abrasive solids, is inextricably linked to the precision and meticulousness employed during its manufacturing. At Center Enamel's advanced production workshop, we utilize specialized equipment for the precise cutting, forming, and welding of reactor vessels from high-strength and abrasion-resistant materials. Our skilled welders, certified to international standards, execute welds with precision to ensure pressure containment and structural integrity under demanding operating conditions. The fabrication and installation of the distributor plate, internal cyclones, heat transfer surfaces, and solids handling systems require meticulous alignment and securement to ensure proper fluidization and particle flow. For reactors operating at high temperatures or with corrosive materials, specialized welding procedures and materials are employed. Complementing this advanced machinery and highly skilled workforce is our comprehensive suite of professional testing equipment, which plays an integral role in our stringent quality control processes. This unwavering commitment to precision manufacturing guarantees that our fluidized bed reactor products consistently meet the high standards demanded by our diverse clientele in energy, chemical, and environmental industries.
Unwavering Quality Assurance: Ensuring Optimal Process Performance and Safety
Our dedication to quality extends throughout the entire lifecycle of our fluidized bed reactors, culminating in a rigorous and comprehensive testing system. This system is designed to guarantee that the performance, safety, and material integrity of our products not only meet but consistently exceed stringent domestic and international standards for pressure vessels and process equipment operating with solids and fluids. Our multi-layered testing regime includes:
Material Verification: We conduct thorough material verification tests to ensure that the reactor vessel and internal components are fabricated from the specified materials with the correct chemical composition, mechanical properties (including abrasion resistance), and high-temperature strength.
Welding Inspection: Our skilled welding is subjected to rigorous inspection, including visual examination and Non-Destructive Testing (NDT) such as radiographic, ultrasonic, or magnetic particle testing, to ensure the integrity and strength of all welded joints, critical for pressure containment and structural stability under demanding operating conditions.
Hydrostatic Testing: Each fluidized bed reactor undergoes rigorous hydrostatic testing at pressures significantly higher than the design operating pressure to verify its structural integrity and leak tightness.
Distributor Plate Inspection: We conduct thorough inspections of the distributor plate to ensure proper hole size, spacing, and overall integrity for uniform fluidization.
Internal Structure Inspection: We meticulously inspect the installation and securement of internal cyclones, heat transfer surfaces, and other components to ensure proper function and prevent damage from particle movement.
Solids Handling System Testing: We conduct functional tests of the solids feeding and withdrawal systems to ensure reliable and controlled flow of particulate materials.
Erosion Resistance Evaluation (Material Samples): For applications involving abrasive solids, we may conduct laboratory tests on material samples to evaluate their erosion resistance.
Dimensional Inspection: Thorough dimensional inspections are carried out at various stages of manufacturing to ensure that all components meet the specified tolerances and dimensions for proper assembly and performance.
Final Inspection: A comprehensive final inspection is performed to ensure the overall quality, finish, and completeness of the fluidized bed reactor.
The Cornerstones of Our Fluidized Bed Reactor Manufacturing Expertise:
Our leadership in the China fluidized bed reactor manufacturer landscape is built upon a robust manufacturing process characterized by several key strengths:
Expertise in Design for Complex Solid-Fluid Systems: Our engineering team possesses deep expertise in the design principles of fluidized beds, considering the intricate interactions between solids and fluids to achieve optimal process performance.
Advanced Materials Selection for Harsh Environments: We have extensive experience in selecting and fabricating reactors from materials capable of withstanding high temperatures, pressures, and abrasive solids.
Precision Fabrication of Critical Internal Components: We have specialized capabilities for the precise fabrication and installation of distributor plates, cyclones, and other internal structures crucial for efficient fluidization and particle separation.
Integration of Reliable Solids Handling Systems: We have expertise in integrating reliable and controlled solids feeding and withdrawal systems into our fluidized bed reactor designs.
Comprehensive Understanding of Diverse Fluidized Bed Applications: Our engineering and manufacturing teams have a strong understanding of the specific requirements of various fluidized bed applications across different industries.
Stringent Quality Control for High-Performance Reactors: Our comprehensive quality control system and thorough testing procedures are adapted for the unique challenges of manufacturing and testing reactors operating with solids and fluids under demanding conditions.
Serving Diverse Industries with Reliable and Efficient Fluidized Bed Reactor Solutions:
Center Enamel's expertise as a leading China fluidized bed reactor manufacturer allows us to provide critical process equipment across a wide array of industries:
Petrochemicals: Our fluidized bed reactors are used for catalytic cracking of heavy hydrocarbons, catalytic reforming, and other catalytic processes.
Energy: We provide fluidized bed combustors for efficient and clean combustion of coal and biomass, as well as fluidized bed gasifiers for converting solid fuels into syngas.
Chemicals: Our reactors are used for polymerization of olefins, calcination of powders, drying of particulate materials, and other chemical processes involving solids.
Environmental: We supply fluidized bed reactors for wastewater treatment (e.g., biological fluidized beds), catalytic oxidation of volatile organic compounds (VOCs), and other environmental remediation processes.
Minerals Processing: Fluidized bed reactors are used for roasting, reduction, and other thermal processing of minerals.
A Comprehensive Portfolio of Fluidized Bed Reactor Designs:
Center Enamel possesses the expertise and capabilities to manufacture various types of fluidized bed reactors, including:
Bubbling Fluidized Bed Reactors: Characterized by a distinct bubble phase and well-mixed solids.
Turbulent Fluidized Bed Reactors: Operating at higher gas velocities, leading to increased turbulence and heat transfer.
Fast Fluidized Bed Reactors: Operating at even higher gas velocities, with high solids entrainment and requiring a cyclone for solids recirculation.
Circulating Fluidized Bed Reactors (CFB): Featuring continuous recirculation of solids between the reactor and a cyclone.
Spouted Bed Reactors: Used for processing coarse particles with a central jet of fluid.
Multistage Fluidized Bed Reactors: Featuring multiple fluidized zones for staged reactions or processing.
Center Enamel – Your Premier Partner for Leading Fluidized Bed Reactor Solutions in China
As a national "little giant" enterprise, Shijiazhuang Zhengzhong Technology Co., Ltd (Center Enamel) stands as a leading China fluidized bed reactor manufacturer, driven by a profound commitment to specialization, innovation, and uncompromising quality. Our comprehensive capabilities, encompassing meticulous design tailored for complex solid-fluid interactions, advanced manufacturing techniques for robust construction in demanding environments, rigorous testing adapted for fluidized systems, and a deep understanding of the unique requirements of various industrial applications, ensure that we can effectively address the most challenging fluidized bed processing needs. By choosing Center Enamel, you are partnering with a company dedicated to providing high-performance, efficient, and reliable fluidized bed reactor solutions, backed by decades of engineering expertise and an unwavering commitment to customer success in energy, chemical, and environmental industries. We are proud to be at the forefront of China's fluidization technology, empowering our clients with the critical infrastructure they need for optimized catalytic and reaction processes.